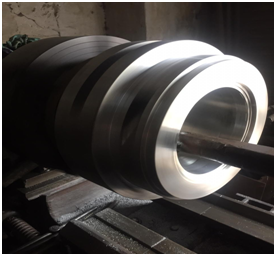
RA Power Solutions having experience of more than 43 years of undertaking manufacturing of New Babbitt Bearing up to 1500 mm diameter. The old bearings that get damaged or worn out are repaired/ rebabbitted using the higher grade of Babbitt white metal & latest process.
Types of Bearings Repair and manufactured by RA Power Solutions:
- Generator bearings
- Turbine Bearing
- Motor Bearings
- Fan Bearings
- Hydroelectric Bearings
- Steel Rolling Mill
- Pump Bearings
- Tilt Pad Bearings
- Trunnion Bearings
- Hydrogen Seals
- Spherical Bags
- Pinion Bearings
- Carrier Bearings
- Compressor Bags
- Guide Bearings
- Ship Bearings
- Thrust Pads
- All other Babbitted Bearings
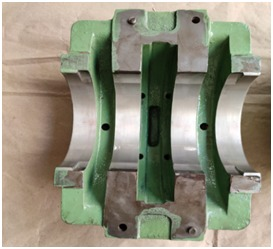

Rebabbitting and Machining Procedures followed by RA Power Solutions
1. Obtain all dimensions and inspect for abnormal or noticeable damage to the bearing shell and surface.
2. Remove the old babbitt and inspect the bonding surface and bearing shell for defects.
3. Prepare a bearing shell before babbitting. We do the shot blasting of the bearing shell.
4. Checking of hardness of bearing shell and removal of hard spots by scooping process.
5. Crack detection of bearing shell by MPI process.
6. If required we also undertake dye penetrant tests and Ultrasonic tests.
7. Cast Babbitt by centrifugal process.
8. Machine splits, assemble bearing, rough machine.
9. Ultrasonically inspect the Babbitt bond.
10. Assemble bearing and finish machine bore and thrust faces.
11. Machine and drill oil reliefs, thermocouples, and oil ports.
12. Prepare bearing for shipper. (deburr, assemble, paint)
13. Record all finished dimensions and file for future service.
14. Package and skid bearings.
15. Follow up with customers to ensure satisfaction.


Industries Served
- Utility Companies
- Steel Mills
- Cement Plants
- Mining Industries
- Motor Repair Shops
- Marine Shipyards
- Military
- Food Processing
- OEM’s
- Transportation
- Irrigation
- Medical
- Agriculture
- Many others, too!
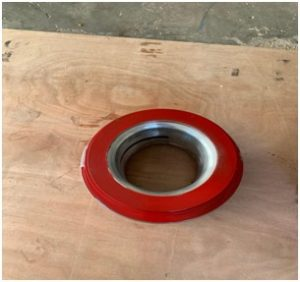
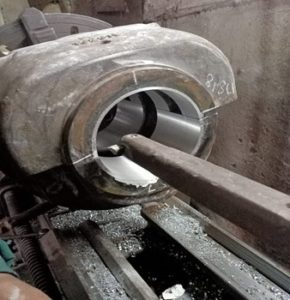
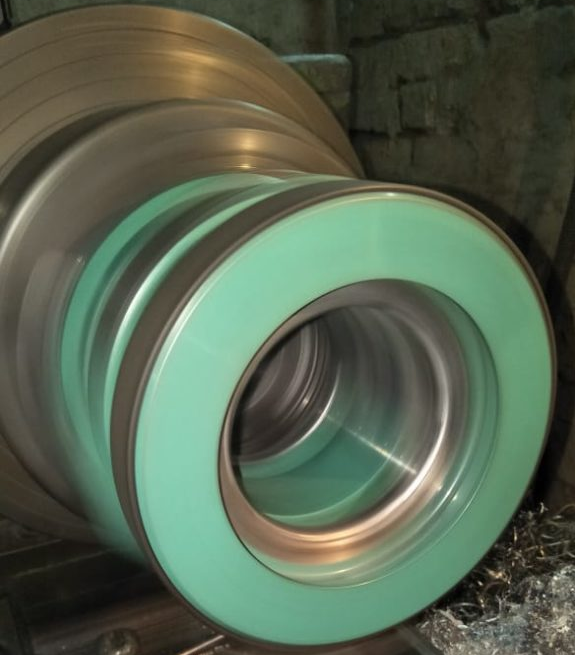
RA Power Solutions is ISO 9001:2015 (Quality Management System) & ISO 14001:2015 (Environmental Management System) certified approved company.
For any repair and maintenance of new bearings, please email us at rajshahani@rapowersolutions.com, info@rapowersolutions.com, or call us at +91 9582647131 or +91 9810012383.